Automated Material Handling
Automated material handling (AMH) continues to revolutionize the way goods and materials are made, moved, packed, stored, and shipped around the world. It continues to evolve through innovations in robotics, AI, machine vision, and RFID technologies.
AMH optimizes logistics and manufacturing operations in several ways. AMH significantly increases efficiency by reducing the need for human labor, enabling faster and more precise material movement. It enhances worker safety, as physically demanding and hazardous tasks can be performed by robots.
AMH increases accuracy by reducing human errors such as picking the wrong item or quantity. AMH helps companies utilize space as efficiently as possible.
AMH and warehouse management systems provide real-time data on operational performance, material flow, and inventory levels. These insights can benefit the entire organization, from procurement to accounting.
Components of AHM systems
The mechanical equipment used in AMH systems includes check-in machines, sorters, conveyors, stackers and unstackers, totes, bins, and trolleys. Somewhere in the process there must be a scanner to read the bar code or a reader to read the RFID tag (or both.)
Conveyors are foundational to AMH systems, utilizing belts, rollers, or chains to move goods between locations in a facility. Conveyors can be straight, curved, inclined, or declined, making them customizable to the materials they transport.
Industrial robots and cobots now have the torque capacity to handle larger payloads for applications such as palletizing and depalletizing. They also have the dexterity, speed, and accuracy for more delicate tasks such as pick and place and packaging products.
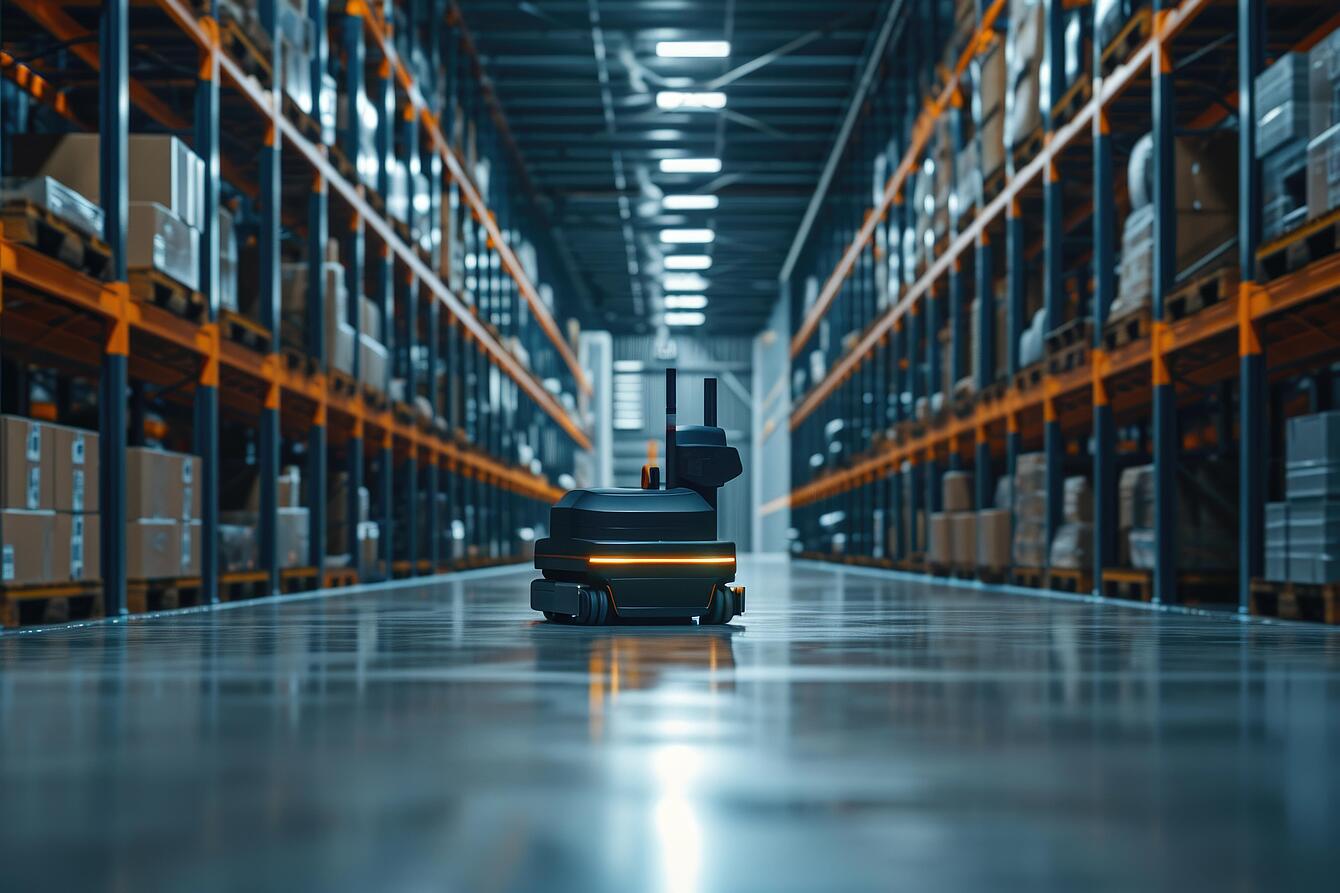
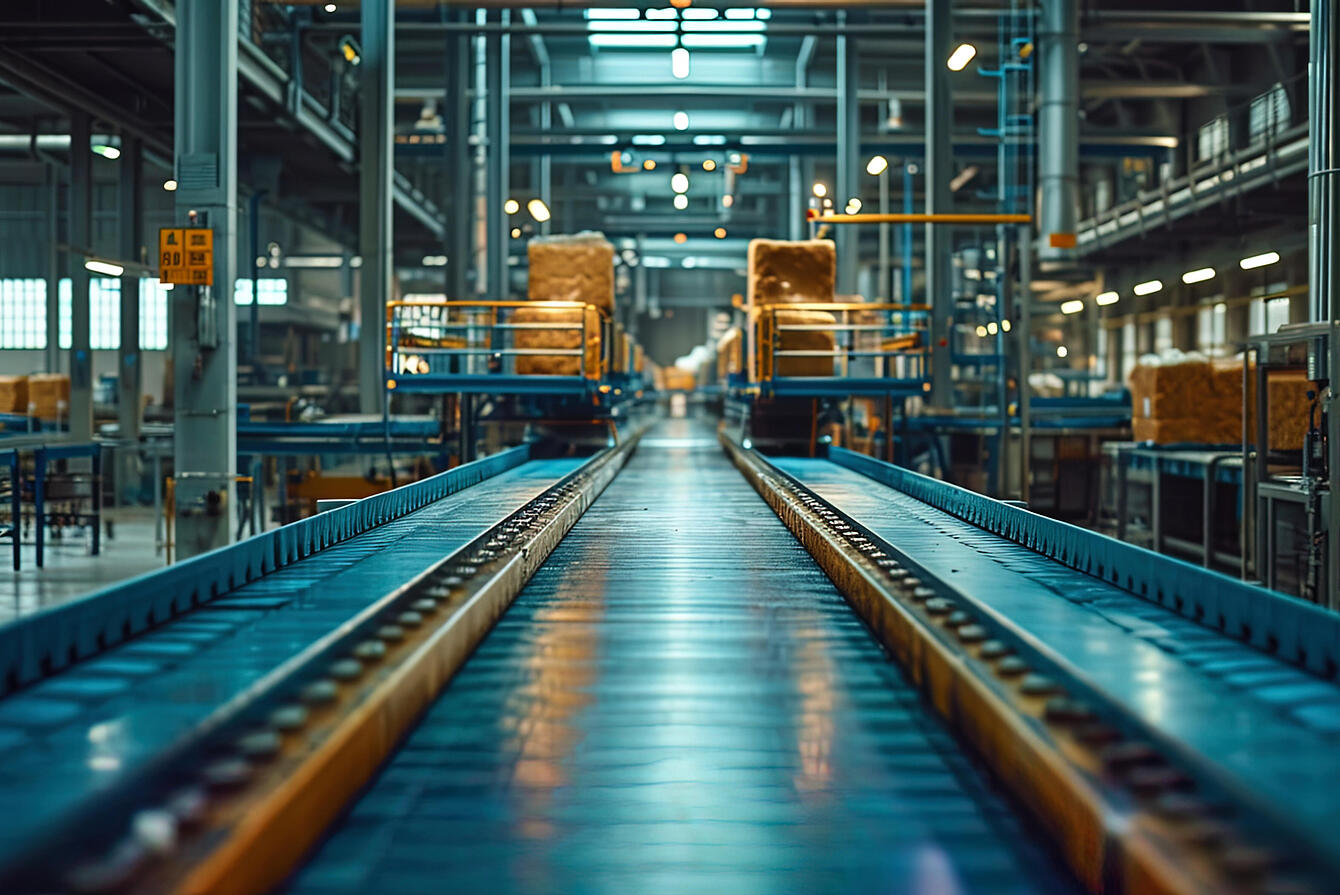
Automated guided vehicles (AGVs) are equipped with guidance systems that enable them to navigate autonomously along predefined paths at a facility. AGVs may follow predefined paths or use mapping technology to direct their movement.
Automated storage and retrieval systems (AS/RS) are a combination of hardware, such as cranes, shuttles, and conveyors, as well as software that controls movement and maximizes storage density.
Warehouse management systems (WMS) are software platforms that control the flow of materials from the time they enter a facility until they are packed and shipped out. A WMS optimizes the entire AMH process through real-time inventory management,
What to know about connectivity in AMH
Electrical connectivity involves the network of electrical systems, components, and devices used to power, control, and communicate within AMH systems. Connectivity is essential for ensuring smooth and efficient operations, as well as enabling data exchange for monitoring, control, and power optimization. In AMH setups, electrical connectivity plays a crucial role in enhancing productivity, safety, and overall system performance. Circular connectors are the essential small pieces and backbone to keep data and power transmission running.
Electrical connectivity involves the distribution of power throughout the material handling facility. Power sources such as electrical panels, circuit breakers, and power cables, let the applications and systems run. Here, circular connectors act as the vital link to transmit the power efficiently. Material handling systems often use electric motors to drive conveyors, cranes, lifts, and other machinery.
Sensors and actuators play a vital role in material handling systems by detecting the presence of objects, measuring distance, or monitoring environmental conditions. Electrical connectivity facilitates the integration of sensors with the central control system, enabling real-time data acquisition and decision-making. Actuators, which perform physical actions based on control signals, are also interconnected to execute various tasks, such as opening and closing gates, activating brakes, or controlling robotic arms.
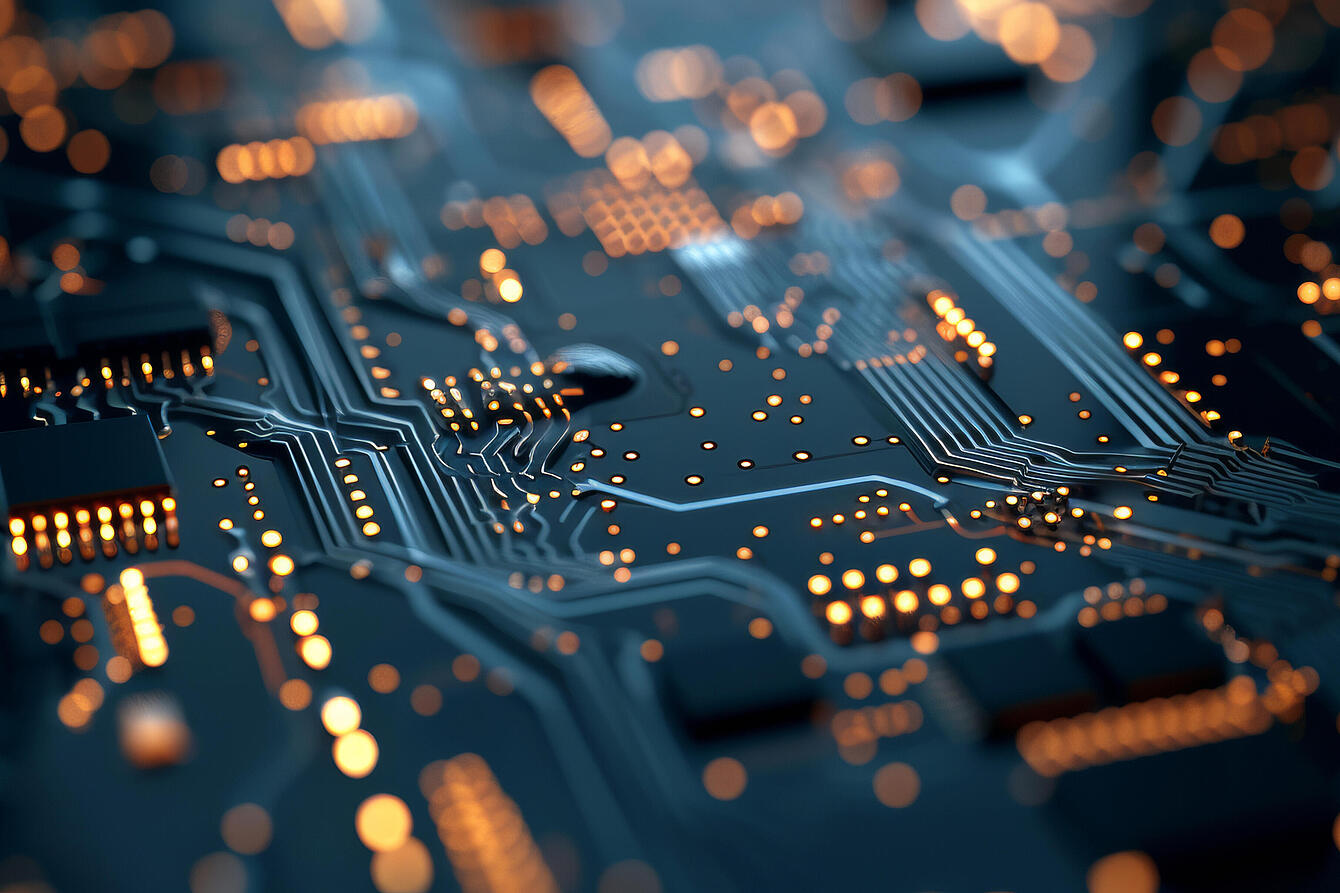
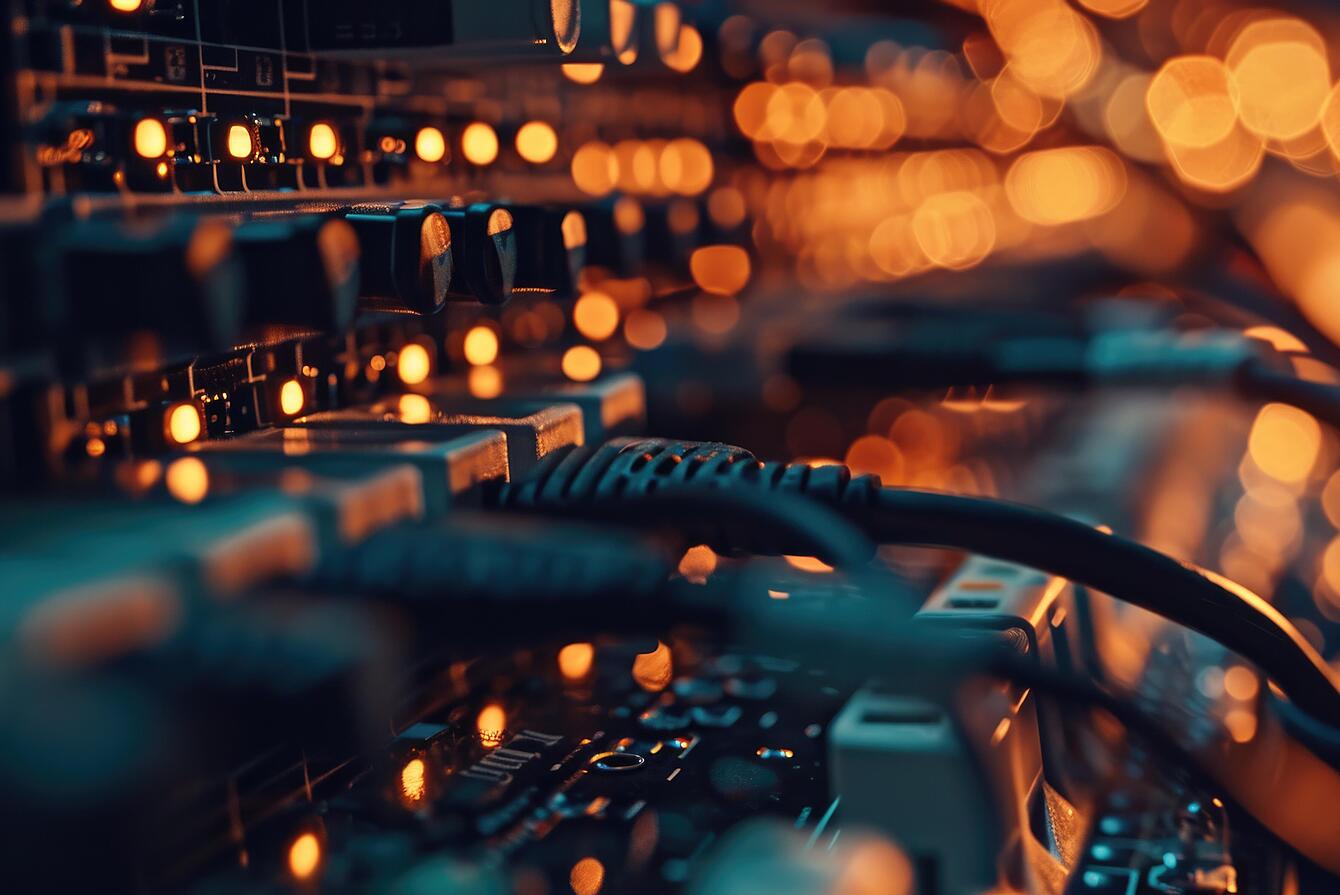
Programmable logic controllers (PLCs) are at the heart of electrical connectivity in material handling. These industrial computers control and automate various processes based on input from sensors. They coordinate the movement of materials, manage traffic flow on conveyors, and synchronize the operation of different machines, enhancing the system's overall efficiency. The information is presented on a Human-Machine Interface (HMI), which provides a graphical user interface that allows operators and engineers to interact with the material handling system. The interface allows personnel to monitor system status, receive alerts, and input commands to adjust settings or address issues.
Material handling systems rely on communication networks for high-speed transfer data between components and systems. Ethernet, industrial protocols such as Profibus or PROFINET, and wireless technologies facilitate seamless data exchange, enabling real-time monitoring, remote diagnostics, and system optimization.
Efficient and reliable electrical connectors are vital for successfully operating AMH systems since they link so many processes. As technology continues to advance, circular connectors will play an increasingly significant role in enabling intelligent, data-driven, and sustainable material handling processes.
Circular connectors in AMH applications
Connectors used in material handling systems must meet several criteria. They must be robust enough to withstand harsh conditions such as extreme temperatures, dusty or moist environments, vibration, and other mechanical stress. Connectors should be constructed from corrosion-resistant materials and have a protection rating of IP67 or higher to guard against dust, moisture, and other contaminants.
A reliable locking mechanism helps to prevent accidental disconnection to ensure stable and secure electrical connection. Connectors should also align with the IEC 60512 standard, and be resistant to shock, vibration, and impact. rough handling, especially if the material handling applications are involved in dynamic movements.
Connectors must provide low resistance and impedance to minimize power loss and ensure efficient energy transmission. They should also have minimal signal interference to maintain reliable data communication. Some applications in material handling require electromagnetic interference (EMI) shielding because they may have sensitive electronic components that can be affected by electromagnetic interference. Connectors with proper shielding can reduce the impact of EMI on nearby electronics.
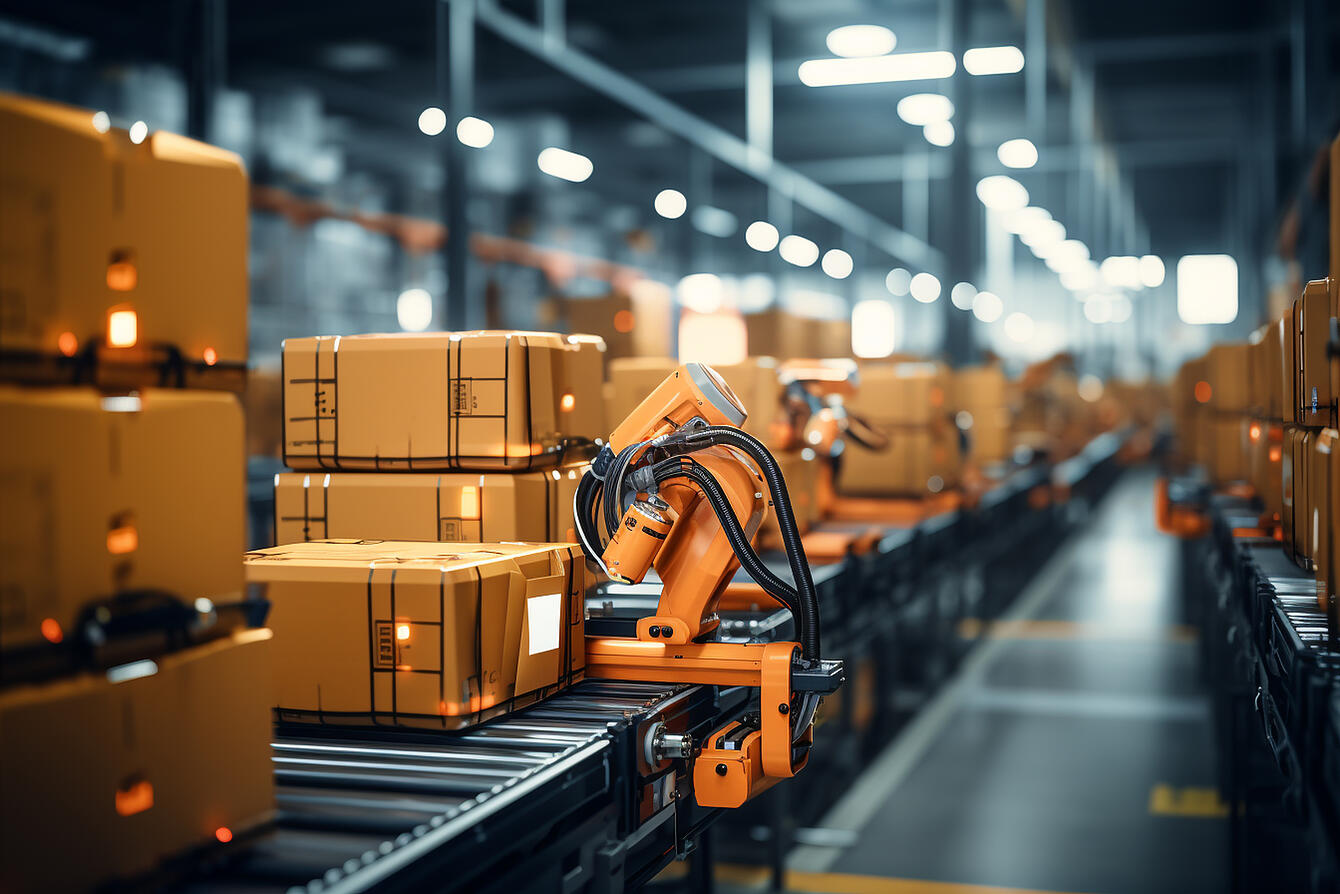
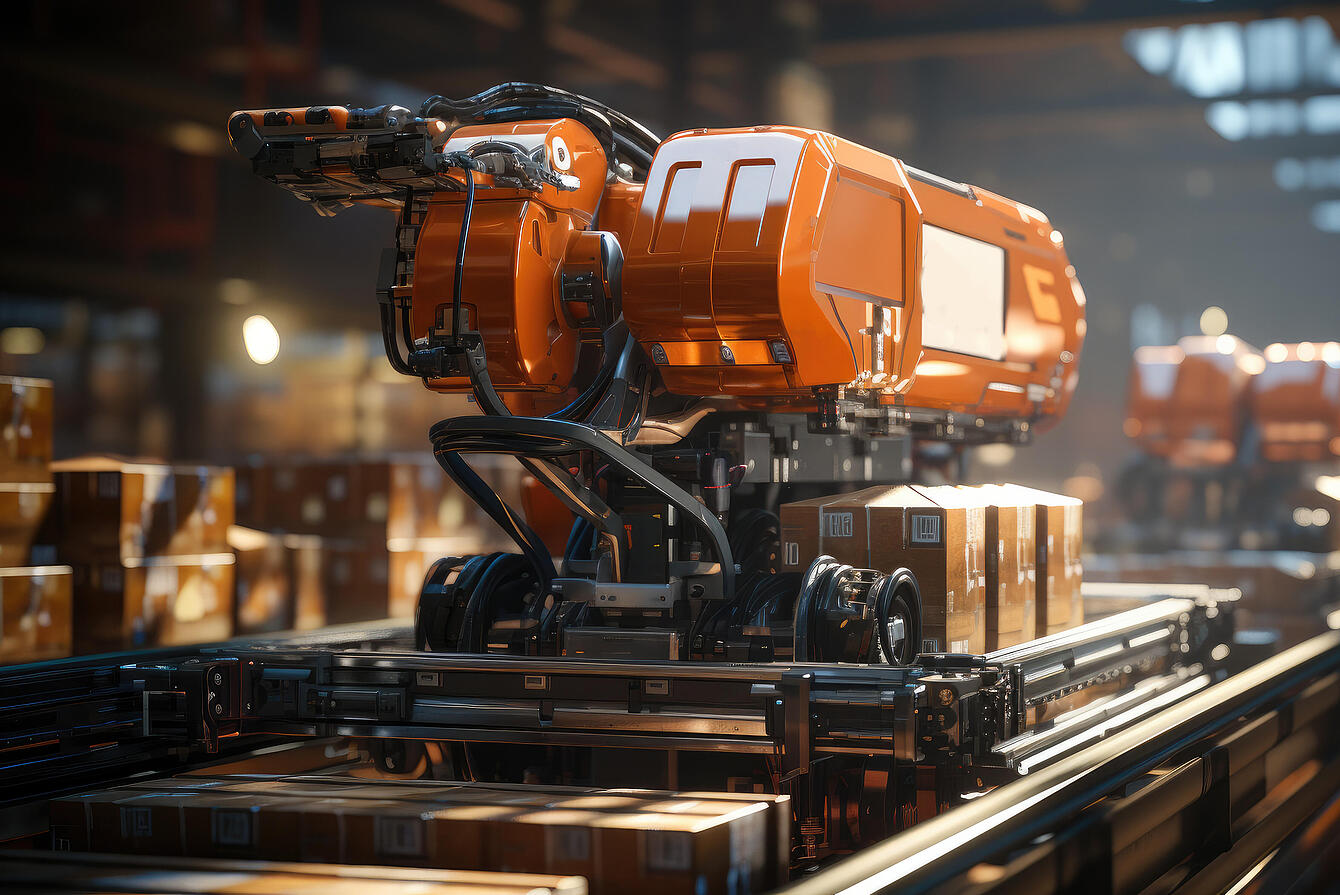
Compatibility in terms of the electrical and mechanical specifications of the equipment is another important aspect to ensure easy integration and interchangeability. Standardized options such as the M12 connector are a good choice. The installation should be seamless and straightforward to minimize downtime during maintenance.
Since material handling is applied in various industries, the connectors must comply with relevant industry standards and safety regulations. Examples of such certifications include UL, CE, or RoHS, which provide more insight into the connector's compliance. By meeting these essential requirements, connectors in material handling systems can ensure a reliable, safe, and efficient operation, contributing to the overall success of the material handling process.
Material handling connectors from binder
Our versatile product portfolio offers many products that could be designed in applications as part of AMH. Based on past customers who frequently used specific product series for material handling applications, we decided to point out the most commonly used series. Please understand that this does not exclude the remainder of our product portfolio, which potentially can also be applied for material handling applications. For more information, please feel free to contact our customer service team (contact@binder-usa.com).
M12-A connector
Its robust design and versatility make A-coded M12 connectors the perfect fit for applications in automated material handling. It has been designed in autonomous mobile robots (AMR), automated guided vehicles (AGV), conveyor systems, palletizers, and robotic systems. Most commonly, the cordset option is used in material handling; however, the M12-A is also offered in more variants including field-wireables or panel mounts. binder's 713 and 763 Series are very versatile and cover many individual customer needs.
Additional features and options of M12-A connectors include:
- Pin count: 3,4,5,8,12
- Gender: male, female
- Version: straight, angled
- Termination style: molded on cable, solder, single wires, screw clamp, wire clamp, IDC, crimping, with cable assembled
- Field attachable, panel mount, and over-molded cordset available
- Shielded options: Shielded, unshielded, shieldable
- Housing material: metal, plastic, plastic LED, stainless steel
- Locking material: metal plastic, stainless steel
- Contact plating material: Au (gold)
- Degree of protection: IP67, IP68, IP69K
- Cable length: 0.3m-10m, other lengths upon request available
- Cable jacket types include PUR, PVC, Special TPE, TPE
- Approval: UL, Ecolab, VDE
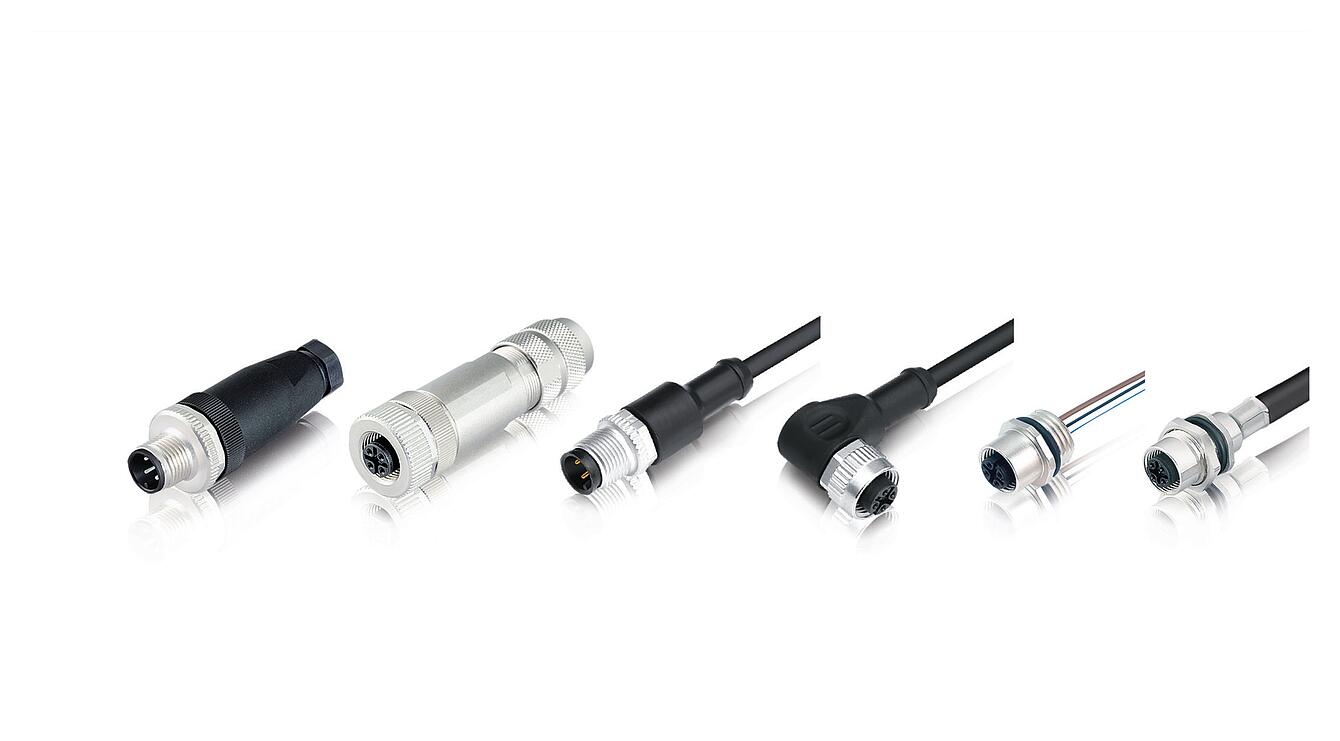
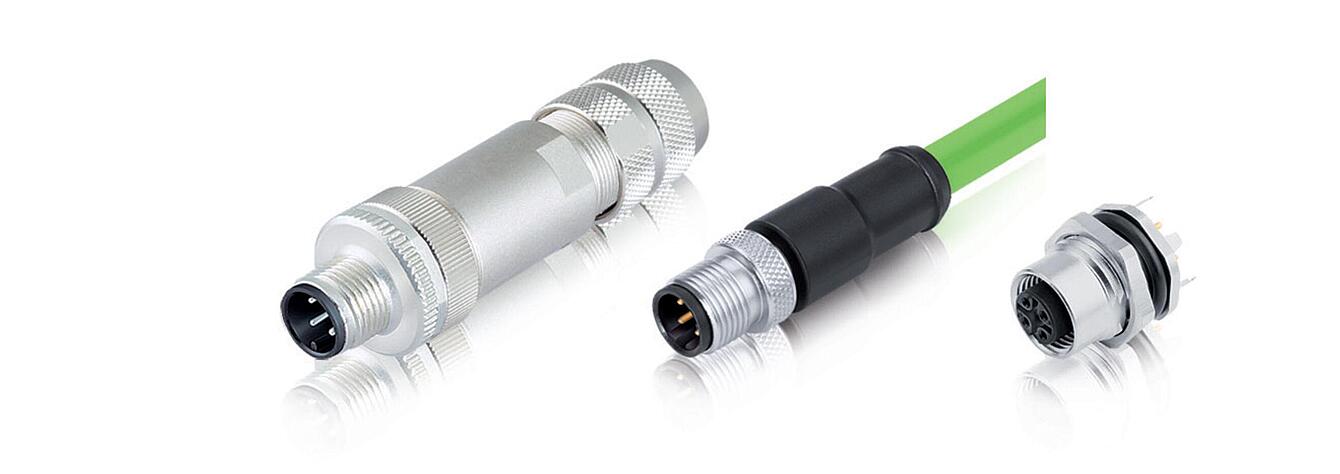
M12-D connector
M12 connectors with D-coding (825/876 series) are a great fit for applications used in material handling as well because of the excellent shielding, high IP rating, and high versatility. The connectors suit high-performance applications that use PROFINET and Ethernet communication protocol with a screw/cutting terminal connection able to reach Cat5. There are several robot systems, AGV, palletizers, and AMR with integrated D-coded M12 connectors. Cable connectors are also available with moulded cable, and panel mount connectors have solder and dip solder connections.
Additional features and options of M12-D connectors include:
- Pin count: 4
- Gender: male, female
- Version: straight, angled
- Termination style: molded on cable, solder, single wires, screw clamp, wire clamp, IDC, crimping, with cable assembled, pluggable
- Field attachable, panel mount, and over-molded cordset available, lead-through for control cabinet
- Shielded options: Shielded, unshielded, shieldable
- Housing material: metal, plastic, stainless steel
- Locking material: metal, plastic, stainless steel
- Contact plating material: Au (gold)
- Degree of protection: IP67, IP69
- Cable length: 0.3m-10m, other lengths upon request available
- Cable jacket types include PUR and TPE
- Approval: UL
M12-X connector
The M12-X connector of the 825/876 series is another product that is suitable for high-performing material handling applications that use PROFINET and Ethernet communication protocol. In the past, X-coded connectors have been designed in AMR, AGV, conveyor systems, and other robot systems. M12-X is a versatile product series including excellent shielding options and a high level of protection. Connector types come in field-wireable options, cordsets, and panel mounts with solder as well as dip solder connections able to reach Cat6A.
Additional features and options of M12-X connectors include:
- Pin count: 8
- Gender: male, female
- Version: straight, angled
- Termination style: molded on cable, solder, IDC, with cable assembled, pluggable
- Field attachable, panel mount, and over-molded cordset available, lead-through for control cabinet
- Shielded options: Shielded, shieldable
- Housing material: metal, plastic
- Locking material: metal
- Contact plating material: Au (gold)
- Degree of protection: IP67, IP68
- Cable length: 0.5m-10m, other lengths upon request available
- Cable jacket types include PUR
- Approval: UL
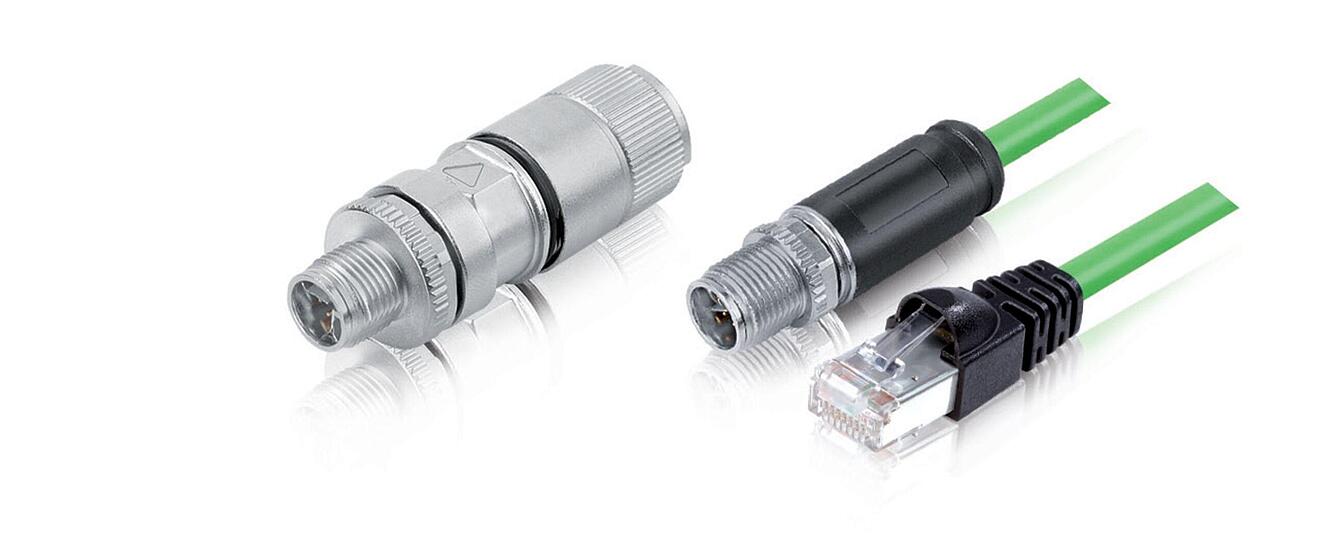
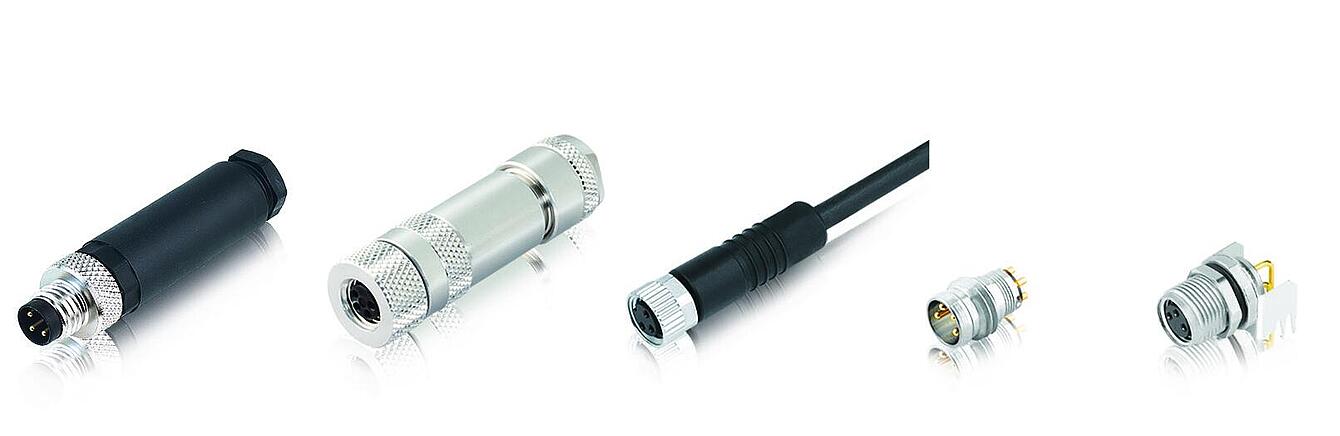
M8 connector
The smaller M8 connector can also be a great fit for AMH applications. Especially, design-ins in conveyors are very common due to its robust as well as space-efficient design enabling to withstand harsh environments in industrial settings. Protection class of IP67 or higher make this possible. The M8 comes with several shielding options, iris spring and shielding rings which ensure reliable EMC shielding.
Additional features and options of M8 connectors include:
- Pin count: 3,4,5,6,8,12
- Gender: male, female
- Version: straight, angled
- Termination style: molded on cable, solder, single wires, screw clamp, wire clamp, IDC, with cable assembled
- Field attachable, panel mount, and over-molded cordset available
- Shielded options: Shielded, unshielded, shieldable
- Housing material: metal, plastic, stainless steel
- Locking material: metal, stainless steel
- Contact plating material: Au (gold)
- Degree of protection: IP65, IP67, IP68, IP69K
- Cable length: 0.5m-10m, other lengths upon request available
- Cable jacket types include PUR, PVC, TPE
- Approval: UL
M8-D connector
The M8-D connector is mainly designed for sensors and actuators in small spaces which makes it a perfect fit for AMH applications. D-coded M8 connectors are available as cable connectors, panel mount or field-wireables. The products are ideal for Industrial Ethernet applications with communication protocols such as EtherNet/IP or PROFINET. Its space-saving design and capability of handling data rates of up to 100Mbit/s makes it suitable for AMH applications demanding Ethernet connectivity.
Additional features and options of M8-D connectors include:
- Pin count: 4
- Gender: male, female
- Version: straight, angled
- Termination style: molded on cable, dip solder, screw clamp
- Field attachable, panel mount, and over-molded cordset available, lead-through for control cabinet
- Shielded options: Shielded, shieldable
- Housing material: metal, plastic
- Locking material: metal
- Contact plating material: Au (gold)
- Degree of protection: IP67
- Cable length: 0.3m-10m, other lengths upon request available
- Cable jacket types include PUR and TPE
- Approval: UL
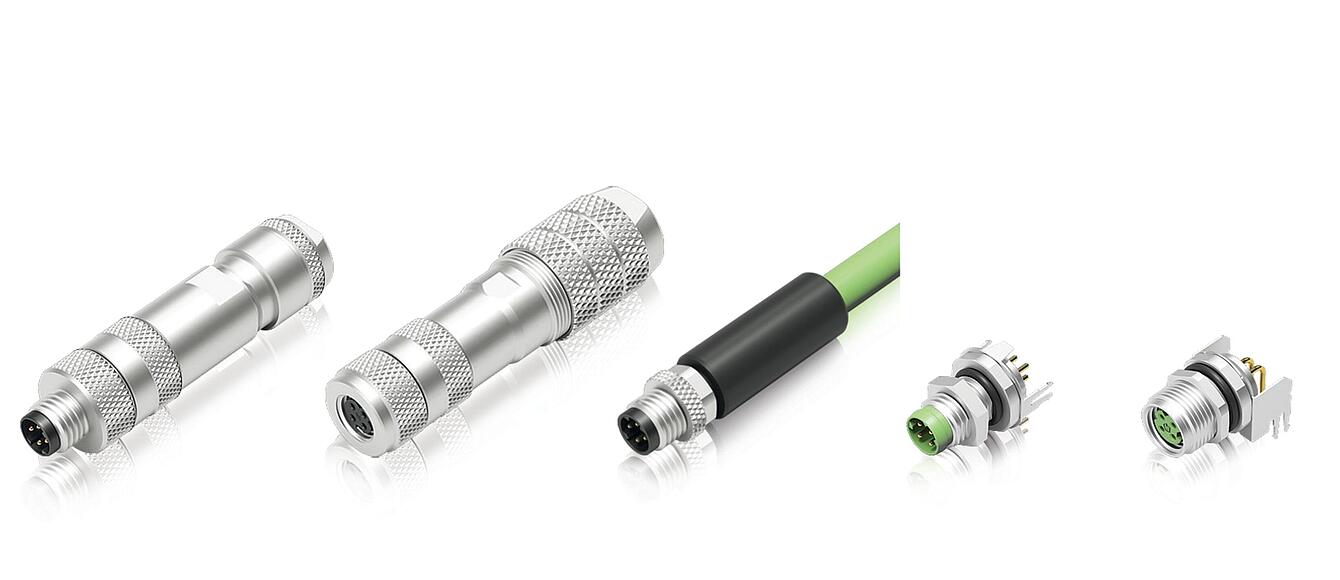
What’s next for material handling automation?
Technologies such as robotics, AI, machine vision, and RFID offer new ways to make AMH even more efficient, cost effective, and sustainable. The same Industry 4.0, autonomous mobile robots, or AI-driven automation are either a direct part of material handling or closely related. Integrating Industry 4.0 technologies, such as the Internet of Things (IoT), artificial intelligence, and big data analytics, is transforming automated material handling systems. Real-time data exchange and intelligent decision-making enable predictive maintenance, optimized workflows, and increased efficiency.